La fundición a través de conformación de moldes tipo cáscara, también conocido como Shell Molding, se puso en práctica por primera vez en la década de los 40 durante la segunda guerra mundial en Alemania por Johannes Croning. Ha crecido de manera significativa, ya que pueden producir a bajo coste muchos tipos de fundición con estrechas tolerancias dimensionales y un buen acabado superficial. El nivel de precisión de las piezas producidas a través de moldeo en cáscara es menor que aquel alcanzado con la técnica de fundición a la cera perdida, sin embargo es mayor que el alcanzado a través de las técnicas convencionales de molde de arena
Moldeo en vacío
es una técnica de moldeo en arena en la que no se emplea ningún aglutinante, ya que la pieza queda suficientemente consistente gracias al vacío creado durante su realización en la caja de moldear. Se trata de una técnica relativamente moderna, ya que surgió en Japón a finales de la década de 1970.
Los diferentes tipos de moldeo en arena son los métodos más empleados en lo que a técnicas de moldeo se refiere, y se caracterizan por el empleo de arena común como material de molde. El procedimiento en estos métodos consiste en la formación de un molde (compuesto por dos piezas) apisonando la arena en torno a un patrón cuya forma será la de la pieza proyectada. A estos moldes, además, se les incorporará un sistema de orificios de colada y de aireación, para así permitir el flujo de metal fundido y minimizar posibles defectos internos en la pieza.

Proceso de poliestireno expandido
Producción de poliestireno expandido. El proceso productivo para la obtención de Poliestireno Expandido utiliza como materia prima el Poliestireno Expandible, el cual se obtiene de la Polimerización del Estireno en presencia de un agente expansor (pentano).
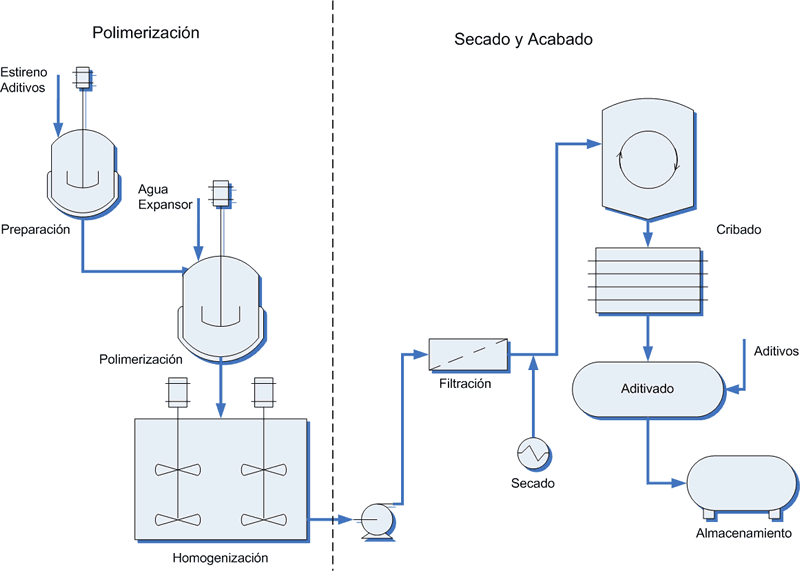
Las piezas que típica mente se fabrican son
impulsores, cortadores para operaciones de maquinado, dados para trabajo en
metal y moldes para la fabricación de componentes de plástico o de hule. Con
este proceso se han fundido piezas con pesos de hasta 700 kg. El Barro es una mezcla de zirconio fino (ZrSiO4),
óxido de aluminio y sílice fundido, que se mezclan con agentes aglutinantes y
se vacían sobre el modelo mismo que ha sido colocado en una caja de moldeo.
El proceso de fundición en molde cerámico, es
similar al proceso de molde de Yeso, con la excepción que utiliza materiales
refractarios para el molde, adecuados para aplicaciones de altas temperaturas.
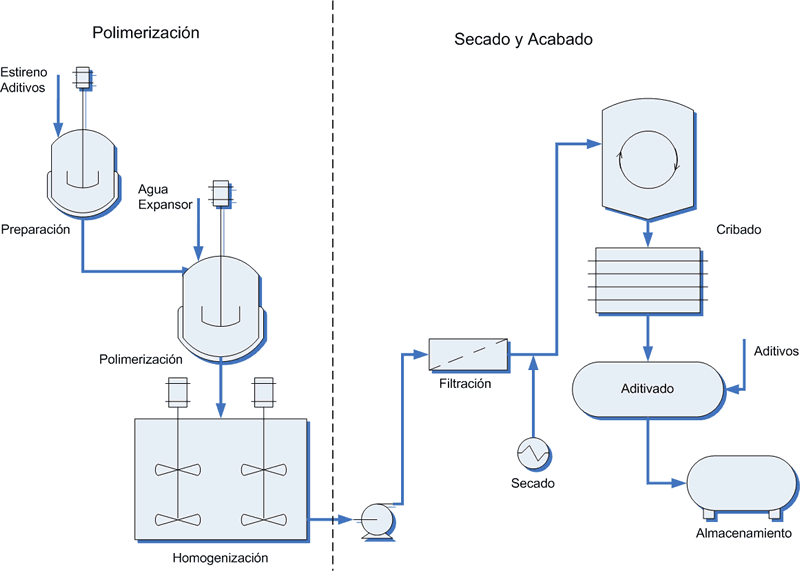
Fundición por Revestimiento.
En la fundición por revestimiento, el
modelo, hecho de cera, se recubre con material refractario para fabricar el
molde, después de esto, la cera se funde y evacua antes de vaciar el metal
fundido. El termino revestimiento viene de la palabra revestir,que
significa “cubrir completamente”, esto se refiere al revestimiento de material refractario
alrededor del modelo de cera.
Fundición de yeso y cerámica
En el proceso Shaw, las caras de cerámica son
recubiertas de arcilla refractaria (arcilla usada en la fabricación de
ladrillos refractarios que resisten altas temperaturas), para impartir
resistencia al molde. Las caras se ensamblan después formando un molde
completo, listo para su vaciado.
Molde de Yeso
Son similares a los de arena, excepto que el molde está hecho de yeso en lugar de arena. Se mezclan aditivos como el talco y la arena de sílice con el yeso para controlar la contracción y el tiempo fraguado, reducir los agrietamientos e incrementar la resistencia. Para fabricar el molde se hace una mezcla de yeso y agua y se vacía en un modelo de plástico o metal en una caja de moldeo y se deja fraguar. La consistencia permite a la mezcla de yeso fluir fácilmente alrededor del patrón, capturando los detalles y el acabado de la superficie. Ésta es la causa de que las fundiciones hechas en moldes de yeso sean notables por su fidelidad al patrón.
Los moldes de yeso no pueden soportar altas temperaturas tan elevadas como los moldes de arena. Por tanto están limitados a fundiciones de bajo punto de fusión como aluminio, magnesio y algunas aleaciones de cobre. Su campo de aplicación incluye moldes de metal para plásticos y hule, impulsores para bombas y turbinas. Las ventajas de los moldes de yeso son el buen acabado superficial.
Los moldes de yeso no pueden soportar altas temperaturas tan elevadas como los moldes de arena. Por tanto están limitados a fundiciones de bajo punto de fusión como aluminio, magnesio y algunas aleaciones de cobre. Su campo de aplicación incluye moldes de metal para plásticos y hule, impulsores para bombas y turbinas. Las ventajas de los moldes de yeso son el buen acabado superficial.
No hay comentarios:
Publicar un comentario